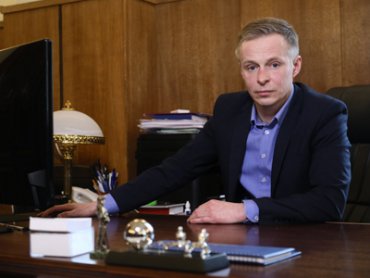
Беседа с директором Института металлургии и материаловедения им. А.А. Байкова Российской академии наук (ИМЕТ РАН), членом-корреспондентом РАН, доктором технических наук Владимиром Комлевым. – Владимир Сергеевич, институт, который вы возглавляете, не так давно отметил 80-летие. Чем он живет, чем дышит? – Институт наш легендарный. Он был основан в 1938 году для решения проблем в металлургической отрасли. Большой вклад институт внес в годы Великой Отечественной войны. В этот период его работа была сосредоточена на освоении новых технологических процессов для производства оборонной продукции, мобилизации ресурсов Урала и повышении мощностей промышленных предприятий. В мае будет 75-летие Великой Победы, и мы в институте также предполагаем проводить празднование в честь этой знаменательной даты. В послевоенные годы институт занимался вопросами восстановления и реконструкции отечественной металлургии, изучением металлургического сырья и определением методов его рационального использования, разработкой новых и совершенствованием существующих металлургических процессов, исследованием физико-химических свойств металлов и сплавов. Сегодня мы работаем в широком спектре разработок в области металлургии и материаловедения, что включает в себя разработки для аэрокосмической отрасли, для автомобилестроения, различные материалы двойного назначения, для сельского хозяйства, нефтяной и газовой отрасли и так далее. Нельзя в принципе найти ту отрасль экономики, в которой наш институт в настоящее время не участвует своими разработками. В каких-то областях мы имеем монополию, где-то решаем только локальные, точечные задачи. Есть очень интересные разработки, допустим, порошки для аддитивного производства. Это металлические, керамические, композиционные порошки, получаемые плазменно-химическими методами обработки. У нас созданы технологии и оборудование для получения таких уникальных материалов, которые могут быть использованы для аддитивного производства. – Для чего эти порошки используются? – Для создания газотурбинных двигателей, лопаток для авиационной отрасли. Есть разработки уплотнения материала до высокой плотности после 3D печати, которая близка к теоретической. Это обработка при высоких давлениях и температурах. Допустим, нужно создать лопатку для двигателя со сложной формой и высокими механическими характеристиками. Требуется сначала синтезировать специальный порошок, воспроизвести форму изделия на 3D принтере и подвергнуть постобработке – высокому давлению и температуре. Для этого теоретическая плотность должна быть практически 100 % или стремиться к этому показателю. Здесь требуются специальное оборудование, подходы, режимы обработки, чтобы создать такой материал. Мы, в частности, работаем с некоторыми предприятиями в этом направлении. И, можно сказать, создаем лабораторные и опытно-экспериментальные партии для использования, например, в авиации. Но не только в авиации – повторю, мы работаем практически во всех отраслях экономики, которые связаны с материаловедением. Мы биологические существа, но всегда взаимодействуем с материалами. Например, мы облачены в одежду. Одежда состоит из материала. Для того чтобы она была надежная, эффективная, безопасная – тоже нужна наука о материалах. Мы используем автомобильный транспорт для передвижения. В нем очень много различных материалов – от алюминиевых сплавов до различных органических добавок в топливо, т.е. наука о материалах – это всё, что окружает наш мир. Считаю, что наш институт является флагманом в материаловедении. Он никогда не останется без работы. Всегда какие-то задачи, которые стоят перед страной, будут ставиться перед нами, и мы будем готовы их решать, потому что у нас замечательный коллектив. Объем знаний, который у нас накоплен, очень велик. И молодежь, которая приходит к нам работать, всегда находит, чему поучиться у наших ветеранов. Мы пытаемся найти определенный синергизм, чтобы этот опыт постепенно переходил молодому поколению. – Давайте вернемся к тем направлениям, которые у вас имеются. Чем еще можете похвастаться? – Спектр работ очень широкий. Это, например, переработка шлаков металлургических отходов, разработка конструкционных сталей различного назначения, магнитных материалов, биоматериалов для реконструктивно-восстановительной хирургии и тканевой инженерии и т.д. У нас создаются сверхтвердые конструкционные материалы, немагнитные и коррозионностойки стали, для нефтедобывающей отрасли. Проводим работы, в том числе, по разработке месторождений. На эту тему с группой компаний «РУСТИТАН» и институтом, при содействии Российского союза промышленников и предпринимателей, подписано соглашение о сотрудничестве по реализации инвестиционного проекта «Строительство вертикально-интегрированного горно-металлургического комплекса по переработке титановых руд и кварцевых (стекольных) песков Пижемского месторождения» и комплексном освоении титановых месторождений в Республики Коми. Институт, обладающий опытом применения экологически чистых технологий замкнутого цикла по получению высококачественного титанового сырья, в рамках реализации проекта разработал технологии переработки титановых руд Пижемского месторождения до получения высокосортных титановых концентратов и извлечения содержащихся в руде редких и редкоземельных металлов. Для сельского хозяйства мы разрабатываем различные кормовые добавки на основе оксидных систем. Допустим, если добавлять оксид железа в различных формах, то он способствует увеличению урожая. Или, если добавлять его в продукты питания животных, у животных увеличивается масса. Особую проблему представляет разработка новых материалов медицинского назначения, предназначенных для контакта со средой живого организма. Еще более востребованы специализированные биосовместимые изделия для сформировавшегося в последние годы нового направления – регенеративная медицина, связанного с разработкой биоискусственных тканей. Институт ведет активные исследования и в данной области. – Эти работы где-то внедряются? – Мы создали несколько малых инновационных предприятий, цель которых – создать производство экспериментальных разработок института, например, кормовых добавок для сельского хозяйства, основанных на синтезе коллоидных растворов оксидов, в том числе оксида железа. Мы пытаемся внедрять свои результаты, а не только заниматься фундаментальными разработками. Фундаментальная наука – это основа, это кирпичики, из которых потом вырастает всё здание. Но прикладные задачи, так как мы материаловедческий институт, мы тоже беремся решать. У нас создан реестр разработок, готовых к внедрению. На сегодняшний момент у нас 473 проекта. Многие из них я беру под личный контроль, курирую. – Одна из основных тем вашего института связана с медициной. Почему институт металлургии, казалось бы, не имеющий прямого отношения к медицине, начал этим заниматься? – Наш институт имеет прямое отношение к разработке медицинских изделий. Допустим, имплантаты из титана широко применяются в травматологии и ортопедии. Поэтому исторически в институте проводились работы по созданию таких материалов. Например, разработка аддитивной технологии формирования биосовместимых композиционных 3D плазменных покрытий титан – титан на поверхности внутрикостных имплантатов. Другой аспект: в 2008 году путем реорганизации Институт проблем керамических материалов Российской академии наук был присоединен к Институту металлургии и материаловедения им. А.А. Байкова. А Институт керамики тоже занимался медицинскими материалами. Объединение дало толчок для развития этого направления – создания более широкого спектра материалов для медицины. Лично моя группа, которой я руковожу, занимается, в основном, материалами на основе керамики, полимеров и композиционных материалов для тканевой инженерии. Наибольших успехов мы достигли в тканевой инженерии костной ткани, потому что костная ткань – это, по сути, керамический материал. Он состоит из 70 % неорганической составляющей. Химики синтезировали этот материал, хотя приблизить его к нативной ткани человека достаточно сложно. Есть много особенностей, подводных камней. Но создать такой материал возможно. И поэтому за последние двадцать лет темой работы моей и моих коллег было как раз создание различных материалов для тканевой инженерии костной ткани. – Какие результаты? – Достигнуты достаточно большие успехи в этом направлении, есть и мировое признание. Нас знают за рубежом, в Европе, на азиатском континенте. Мы пытаемся создать синтетический аналог тканевого эквивалента, и для этого используем различные подходы, в том числе, аддитивное производство, т.е. 3D-печать. Например, нам нужно создать из неорганики фосфатов кальция какой-то трехмерный биосовместимый объект сложной геометрии, с внутренней архитектоникой, взаимосвязью пор и так далее, наиболее близкий по архитектуре и по фазовому химическому составу к костной ткани. Как мы это сделаем? – А для чего это нужно делать? Для того чтобы заместить какие-то костные дефекты, полученные в результате травм, операций, лучевой терапии и так далее? – Да, особенно, в случаях критического размера. Так вот, наибольшего успеха мы добились в создании оборудования, способа и технологии производства таких матриксов, или имплантатов, для тканевой инженерии, которые основаны, например, на реакционном связывании при физиологических температурах. Что это такое? Керамика известна тем, что традиционно нужно ее нагреть до 1000-1200 градусов. Но в нашем теле такого же не происходит. В нашем теле температура около 37 градусов. Все процессы формирования костной ткани должны проходить при этой температуре. Было достаточно сложно найти условия формирования таких материалов и создать соответствующее оборудование. Но мы это сделали. В частности, в сотрудничестве с ФНИЦ Кристаллография и фотоника Российской академии наук, МНИОИ им. П.А. Герцена – филиал ФГБУ «НМИЦ радиологии» Минздрава России и ПАО ИСКЧ разработаны материалы и технологии 3D печати персонализированных конструкций с остеогенными факторами как для направленной регенерации костной тканей, так и других тканевых эквивалентов для решения многих проблем в области ортопедии, стоматологии, челюстно-лицевой хирургии, нейрохирургии, онкологии в ближайшей перспективе. – Что представляют собой остеогенные факторы? – В основном, для них используют мезенхимальные мультипотентные стволовые клетки. Можно пойти по другому пути – использовать генные конструкции, которые передают информацию, в нашем случае эндотелиальный фактор роста, который, условно, будет передавать клетке информацию. Механизм действия генных конструкций заключается в высвобождении из структуры носителя, поступлении в клетки-мишени (в области костного дефекта), экспрессии в них, в результате которой клетки начинают работать как «биореакторы» терапевтического белка (кодируемого генной конструкцией), который в свою очередь и обеспечивает биологический эффект. Клетка формирует сосуды, а сосуды нужны для питания. Таким образом, мы создали трехмерный объект под заданный дефект костной ткани. В этот объект поместили генную конструкцию. – И он там развивается, растет и делает то, что нужно? – Если говорить упрощенно, то да. Хирург имплантировал – и всё выросло само. – Потрясающе. – На первой ступени генные конструкции попали в клетки самого организма. Они передали информацию, что нужно, допустим, создать условия для ускоренного ангиогенеза и васкуляризации. Создали сосуды. Поток питательных веществ подошел к дефекту. Таким образом, синтетический материал обеспечен определенными факторами, после чего с течением времени он растворяется, а на его месте образуется нативная ткань пациента. Это классический сценарий в очень упрощенной форме. – Неужели всё идёт без сучка и задоринки? – Конечно, есть определенные сложности, например, кинетика биодеградации материала может быть не сопоставима с остеогенезом. Иначе говоря, может быть недостаточна скорость биодеградации. Но это постепенно решается скрупулезной работы, шаг за шагом. – Нашло ли это как бы такой какое-то клиническое применение? – Здесь у нас тоже есть малое инновационное предприятие в институте, которое было создано еще пять лет назад. В нем зарегистрировано два медицинских изделия, которые применяются, в основном, в стоматологии. Для травматологии и ортопедии объемы нужны большие, а стоимость должна быть меньше. Здесь играет роль коммерческая составляющая, ничего больше. – Но вы же наверняка не собираетесь останавливаться на стоматологии? – Не собираемся. В партнерстве с ПАО ИСКЧ создан первое в мире генно-активированное медицинское изделие. Оно прошло клинические испытания в прошлом году и зарегистрировано Росздравнадзором. Это уникальный случай. Буквально два дня назад мы направили в один из журналов с очень высоким рейтингом статью на эту тему. Заголовок – «Первое в мире применение генно-активированного препарата в клинической практике». – Что же это клиническое применение показало? – Показало высокую эффективность. Этот изделие тоже применяется для тканевой инженерии костной ткани. В стоматологии, челюстно-лицевой хирургии, нейрохирургии, травматологии, ортопедии он незаменим. Исследование проведено по стандартам GPA, Federal Drug Administration. Была большая создана группа пациентов с различными заболеваниями костной системы, начиная от проблем синуслифтинга до замещения различных критических и протяженных дефектов костной ткани. Пациенты наблюдалась в долгом периоде времени. Там больше двадцати или тридцати пациентов за несколько лет под серьезным наблюдением. Им делали компьютерную томографию, заборы слюны, проводили анкетирование, визуальный осмотр, даже брали биоптаты, чтобы провести гистологическое исследование и посмотреть, как формируется костная ткань в течение времени. Результаты показали, что практически 100 % получили полное восстановление. Доказано, что изделие безопасно и эффективно. И оно является единственным не только в нашей стране, но и в мире зарегистрированным генно-активированным препаратом для данной области медицины. Но мы пошли дальше. С лабораторией 3D Bioprinting Solutions, также которые интересуются тканевой инженерией, мы разработали подходы создания трехмерных конструкций с использованием левитации. – Левитации? Это уже что-то мистическое. – Да, почти. Звучит интригующе. Но это чистая наука. Аддитивное производство или, по-другому, 3D-печать заключается в чем, что послойно формируется образец. Слой за слоем с какой-то дельтой – допустим, 50, 100 или 500 микрон (это зависит от разрешения оборудования) формируются слои. Таким образом, «выращивается» объект. А мы подумали – нельзя ли сделать так, чтобы взять частицы микронного или субмикронного размера, поднять их в воздух и собрать трехмерную конструкцию? – В воздухе? – Да, в воздухе или в какой-то среде. И это нам удалось. 4 марта была опубликована наша статья с коллегами в «Scientific Report» о том, что был создан новый подход в нашей области – биофабрикация. Мы называем её биофабрикация трехмерной конструкции с использованием эффекта левитации. Все происходит по принципу лепки снежка. Частицы поднимаются и потом собираются в конструкцию, которая задается определенной программой. Пока это только первые опыты, пробные подходы. Но я считаю, что это направление может иметь очень интересное развитие. Вы не делаете это послойно, а берете и собираете сразу. Знаете, как в фантастических фильмах зарубежного производства, когда какие-то кубики взлетают, а потом собирается некая сложная конструкция. Вот такую вещь мы осуществили. Конечно, пока на маленьких лабораторных образцах, но это действительно работает. – Выходит, левитация вполне возможна? – Конечно. Левитацию можно создать. Как? Первое – это с использованием магнитных полей, когда мы используем, допустим, парамагнетики, поднимаем и присоединяем частицы друг к другу, и у нас собирается конструкция. Либо в условиях микрогравитации. Здесь с нашими партнерами (3D Bioprinting Solutions, ГК Роскосмос) мы отправили партию образцов на Международную космическую станцию (МКС). Недавно проводились эти эксперименты. 3D Bioprinting Solutions совместно с ГК Роскосмосом в 2018 году направили туда (МКС – прим. Редакции) оборудование, которое дает возможность фабрикации таких конструкций. А мы подключились к этой работе, и в августе 2019 года первые экспериментальные образцы были направлены на МКС с Байконура. Я там сам присутствовал, смотрел, как это все собирается, загружается в космический корабль, как ракета улетает. Зрелище, конечно, потрясающее. Хотя бы раз в жизни это нужно посмотреть. А в сентябре был последний старт с Гагаринского старта. Тоже была направлена партия наших образцов. Космонавты проводили эксперименты, эти образцы потом были возвращены на Землю, доставлены в г. Королев, потом к нам. Сейчас мы провели их всестороннее исследование. – То есть, по сути, на орбите были собраны костные ткани? – Да, с использованием левитации. Ведь там практически отсутствует гравитация. То есть эффекты, которые происходят там, радикально должны отличаться от земных. И мы создали конструкты. Сначала провели эксперименты по рекристаллизации самих фосфатов кальция, выяснили, как они взаимодействуют, как формируют трехмерный объект. Это была первая часть эксперимента. На втором этапе проходила рекристаллизация фосфатов кальция, то есть создавался неорганический каркас, и к нему подсоединялись сфероиды (клетки). У нас получился бионеорганический конструкт. Грубо говоря, живой. Сейчас мы эти образцы проанализировали совместно с нашими партнерами, с другими академическими институтами и собираемся представить общественности в виде публикации. Я думаю, получится хорошая публикация, может быть, уровня «Nature» или «Science», потому что это первая работа, когда тканевые конструкты были собраны в приблизительно 400-500 километрах от Земли. – Если экспериментальный образец можно собрать на МКС, то для широкого потребления вряд ли получится производить такие конструкции. Как вы будете решать эту проблему, если такие изделия потребуются в большом количестве? – Их можно сделать в земных условиях, используя, допустим, биофабрикацию в магнитных или акустических полях. Но почему мы проводим эксперименты на МКС? Потому что там практически отсутствует гравитация. Здесь мы обращаемся как раз к фундаментальным исследованиям. Проводя эти исследования в принципиально отличных от земных лабораторных условий, мы можем найти что-то новое, ранее неизвестное. – И потом использовать это на Земле? – Это можно потом перенести на земные условия. Либо предположить, что все-таки развитие науки и техники будет достаточно скачкообразным, и «наши корабли скоро будут бороздить просторы вселенной». – Выращивать необходимые материалы для своих целей? – Да. Или, допустим, предполагается, что в ближайшие там 20-25 лет люди осуществят высадку на Марс. Там условия гравитации тоже другие. Может быть, им будет необходима медицинская помощь, и эти фундаментальные знания также пригодятся. – Вы любите фантазировать? – Это фантазии, да. Но любая фантазия, на самом деле, имеет под собой какую-то основу, и, в конце концов, она реализуется в будущем. – Поделитесь еще какими-то научными фантазиями? О чем думаете? О чем мечтаете? – Сейчас очень много административной работы. Так много, что иной раз мечтаешь только об одном – вернуться в науку. Но, с другой стороны, для меня большая честь руководить таким легендарным институтом с таким высоким кадровым потенциалом, с такой талантливой молодежью. Это очень интересно. Очень много потрясающих работ. Я постоянно чему-то учусь. Это тоже важно – не останавливаться на достигнутом, продолжать развиваться. Мне интересны люди ищущие. Пусть даже ошибающиеся. Нельзя знать всё. Но вот приходит к тебе человек с каким-то вопросом – и мы вместе ищем решение, собираем всё воедино, как конструкцию в воздухе, и иногда находим что-то совершенно новое, неожиданное.
Ссылка на сайт |